Quality assurance
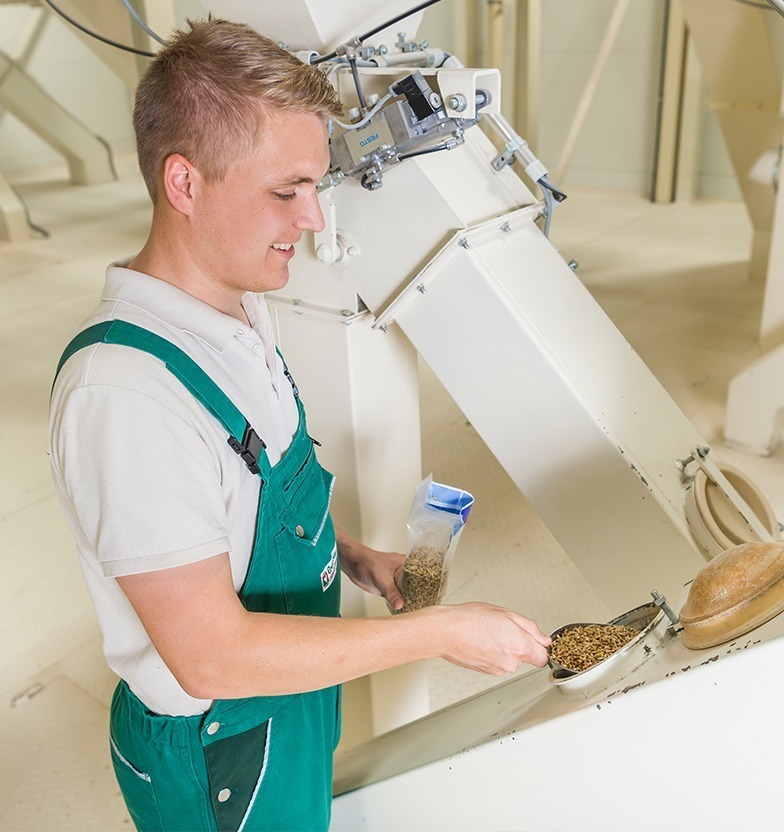
Quality assurance
Feed production is one of the most important factors in the production of animal food. With our quality assurance system, we create the conditions for safe food. Since its introduction, we have met the requirements of various inspection systems, starting with GMP in 1995, ISO 9001 in 1997, and since 2002 with the newly founded QA inspection system. The QA testing system for food is the only testing system in Europe for food spanning from the farmer to the shop counter.
The production of compound feed is embedded in a quality assurance system from the production of raw materials on farms to the retail and delivery of the finished compound feed.
The entire process is subject to strict controls in terms of hygiene, undesirable substances, microbiological quality and transport. All process steps are analysed, evaluated and preventively controlled in the HACCP system. When it comes to hygiene, the main focus is on constant cleaning of all parts of the plant, from the raw material cells to the production line and the finished feed cells. But it also includes the suppliers and the delivering silo vehicles. Preventing undesirable substances requires constant product and process controls in the form of chemical and microbiological analyses. Separate facilities or regulations on the transport sequence are necessary to avoid cross-contamination. HACCP (Hazard Analysis and Critical Control Point) means preventive risk management. Critical control points are defined where appropriate measures are taken to eliminate the risks or reduce them to an acceptable level.
Raw materials, production, products and laboratory analyses
Raw materials
We only receive our raw materials from QA approved suppliers. We are connected to the raw material database of the DVT (German Pet Food Association). Thanks to its rapid alert system we can react immediately to imminent risks. Samples are taken from all deliveries and an incoming goods inspection is carried out. This includes identification, sensory testing, examination for pest infestation and foreign components as well as NIR analyses for nutritional value-determining ingredients such as crude protein. All raw goods at risk of mycotoxins are examined in our own laboratory. Microbiological tests are carried out by external accredited laboratories. Samples are continuously taken at critical points in the production process.

Products
The finished products are continuously tested for their nutritional components (fat, protein, etc.) and for undesirable substances (dioxins, heavy metals, pesticides). Automatic sampling in all production lines guarantee complete quality control of our products. These samples are kept for six months. In the end, a sample is taken from each batch when the feed is loaded.
Our field service team continuously checks the performance of our feed at the customer’s site and inspects the health of the animals. Together with our quality managers, we continuously work on optimising our products.

Production
The entire production process is computer-controlled and monitored – and thus traceable and safe. Hygienisation of the feed by heating it during the pressing process is an essential factor for a microbiologically flawless product. To satisfy the requirements, all parts of the plant are cleaned regularly, from reception to loading. Separate production routes for certain types of feed are just as much a part of the safety system as rinsing batches and carry-over tests.

Laboratory analyses
In our in-house laboratory we use NIR spectrometric analysis to analyse: proteins, fats, fibre content, moisture, ash, starch content and energy content.
Alternatively, we use the Kjeldahl method to analyse protein content; a polarimeter for starch; wet chemical processing for dry matter and ash; ELISA screening for mycotoxins (DON, zearalenone); flame AAS for phophore, calcium, sodium and potassium; sieve analysis according to ISI 3310-1 for pH value and grain sizes; the calibrated granomat meter for HKL weight and moisture.

Raw materials
We only receive our raw materials from QA approved suppliers. We are connected to the raw material database of the DVT (German Pet Food Association). Thanks to its rapid alert system we can react immediately to imminent risks. Samples are taken from all deliveries and an incoming goods inspection is carried out. This includes identification, sensory testing, examination for pest infestation and foreign components as well as NIR analyses for nutritional value-determining ingredients such as crude protein. All raw goods at risk of mycotoxins are examined in our own laboratory. Microbiological tests are carried out by external accredited laboratories. Samples are continuously taken at critical points in the production process.
Production
The entire production process is computer-controlled and monitored – and thus traceable and safe. Hygienisation of the feed by heating it during the pressing process is an essential factor for a microbiologically flawless product. To satisfy the requirements, all parts of the plant are cleaned regularly, from reception to loading. Separate production routes for certain types of feed are just as much a part of the safety system as rinsing batches and carry-over tests.
Products
The finished products are continuously tested for their nutritional components (fat, protein, etc.) and for undesirable substances (dioxins, heavy metals, pesticides). Automatic sampling in all production lines guarantee complete quality control of our products. These samples are kept for six months. In the end, a sample is taken from each batch when the feed is loaded.
Our field service team continuously checks the performance of our feed at the customer’s site and inspects the health of the animals. Together with our quality managers, we continuously work on optimising our products.
Laboratory analyses
In our in-house laboratory we use NIR spectrometric analysis to analyse
proteins, fats, fibre content, moisture, ash, starch content and energy content.
Alternatively, we use the Kjeldahl method to analyse protein content; a polarimeter for starch; wet chemical processing for dry matter and ash; ELISA screening for mycotoxins (DON, zearalenone); flame AAS for phophore, calcium, sodium and potassium; sieve analysis according to ISI 3310-1 for pH value and grain sizes; the calibrated granomat meter for HKL weight and moisture.
We are certified
The ‘GMP+ BCN-NL1 Antibiotic-free feed’ standard confirms that our production sites are free of antibiotics and that there are no antibiotic residues in our feed.
Our Rothkötter compound feed plants are certified according to the internationally recognised DIN EN ISO 50001 energy management system.